Robots People Want to Work With: The Power of Human-Centered Design
Why trust, comfort, and perception—not just performance—are the real keys to robotics adoption.
Aaron’s Thoughts On The Week
"Design is not just what it looks like and feels like. Design is how it works." — Steve Jobs
When people think about robotics, they often picture the marvel of motion — a robotic arm painting a car, an exoskeleton helping a worker lift a heavy box, or a humanoid robot navigating a busy warehouse. But beneath all the software, servos, and sensors, the most crucial factor in robotics today is not what robots can do — it's how they do it with us.
As robots and exoskeletons move deeper into everyday workspaces, from factories to hospitals to distribution centers, the focus shifts from sheer capability to human-centered design. This softer side of robotics — prioritizing safety, comfort, and trust — is increasingly the deciding factor for future success in our industry.
It's Not Just About Performance Anymore
Early robotic systems were designed with performance as their guiding principle. Could it weld faster? Could it lift more? Could it work longer? These were the questions engineers raced to answer. But as robots began to share workspaces with humans, new questions emerged:
Can it work safely alongside humans?
Does it reduce strain or create new discomfort?
Will workers trust and adopt it?
These questions are fundamentally about design, not just technology. A robot’s success depends not only on its power and precision but also on how it is perceived by the people working alongside it.

The Ergonomics Dilemma: Good Intentions Meet Reality
Exoskeletons exemplify how good intentions often clash with the hard realities of design. Many exosuits claim to reduce lower back stress, minimize shoulder injuries, and alleviate repetitive strain. However, if the exosuit is heavy, restricts movement, or creates new pressure points, workers simply won't wear it.
There's a well-known saying in industrial design circles: "The best tool is the one people actually use." The same applies to exoskeletons and collaborative robots (cobots). Successful designs don't just reduce injuries on paper; they integrate seamlessly into the worker's existing workflow.
This is where design choices are crucial:
Does it limit the range of motion?
Is it adjustable for different body types and tasks?
Can workers easily put it on or take it off during shift changes?
Without clear and thoughtful answers to these questions, even the most promising technology can become an expensive dust collector.
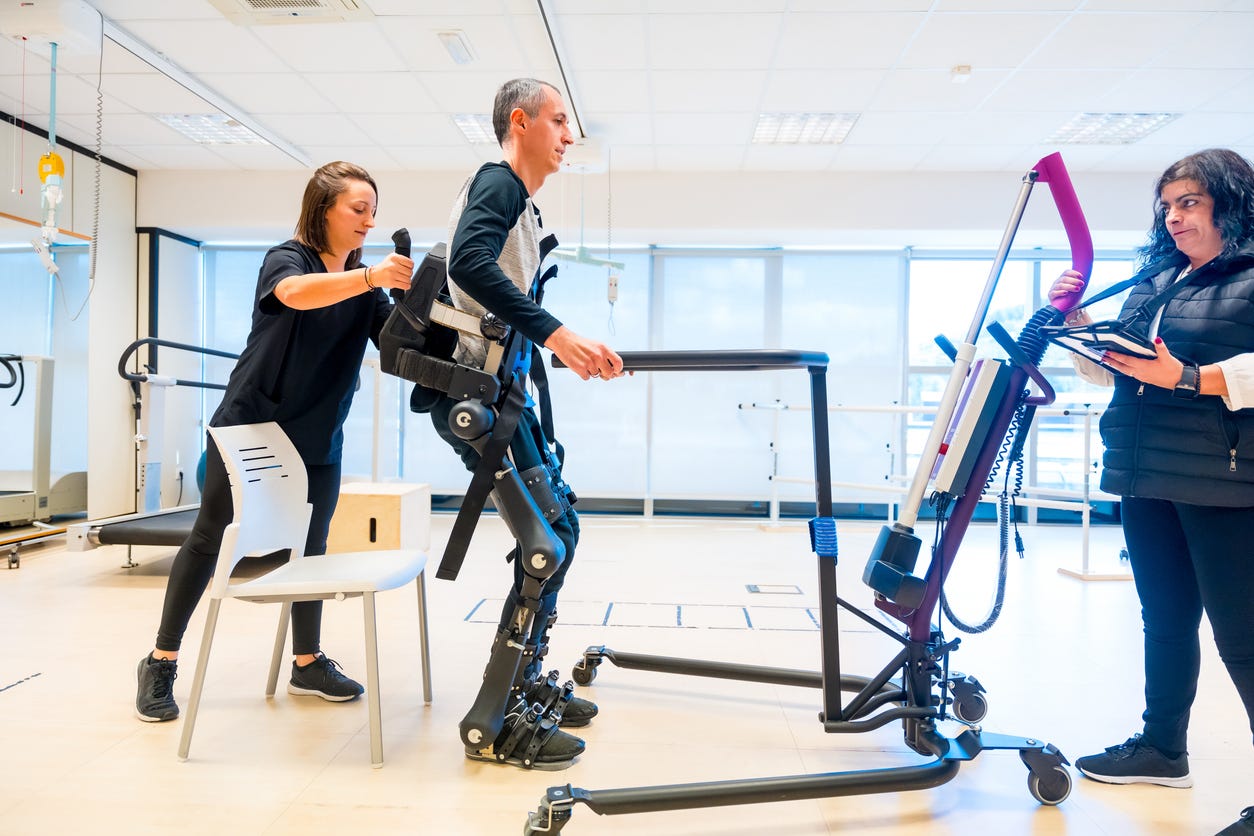
Human-Robot Interaction (HRI): The Trust Factor
Introducing robotics into a human workspace isn’t just a technical integration — it’s a social one. Workers must trust the robot, or it will never be fully embraced.
In How Design Makes Us Think, Sean Adams highlights how visual, physical, and behavioral cues shape our instinctive reactions. This applies directly to human-robot interaction. Humans are susceptible to shape, motion, and expression, even in inanimate objects. In fact, we subconsciously assign personalities to things — even robots.
Designers who ignore this human trait risk creating robots that seem cold, threatening, or unpredictable. Good HRI design leverages this tendency:
Cobots with soft edges and rounded corners appear less intimidating.
Embedded lights or expressive displays can signal intent or readiness.
Haptic feedback or gentle resistance lets workers feel what the robot is doing.
These cues help workers develop trust. The robot becomes predictable, cooperative, and even approachable. Without this, the robot remains “the machine” rather than “my tool.”
Adaptive Control: Following, Not Leading
Another critical enabler of trust in human-robot collaboration is adaptive control. Unlike traditional automation, which follows rigid, preprogrammed motions, modern robotic systems are increasingly designed to sense and respond to their human counterparts. Instead of dictating how tasks are performed, these robots adapt in real-time, allowing the human to lead and the machine to follow.
For example, an industrial exosuit might continuously adjust its assistance based on a worker’s posture, movement speed, or the amount of force they apply. This helps reduce strain without limiting natural motion. Similarly, a surgical robot may sense the subtle pressure exerted by a surgeon and adjust its force or movement to provide precise assistance without overriding the surgeon’s intent. On factory floors and in warehouses, collaborative robots (cobots) are often programmed to pause, slow, or yield when they detect unexpected human movement, prioritizing safety over task speed.
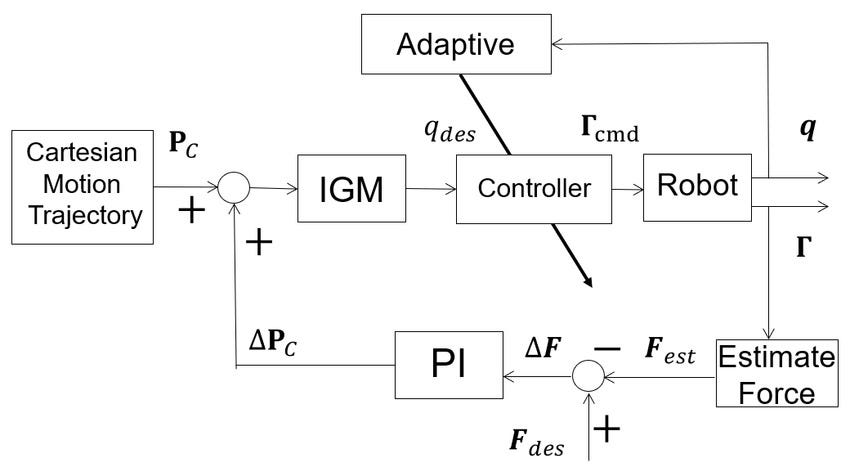
Adaptive control may not be the most visible feature of a robotic system, but it is foundational to building psychological safety — the sense that the robot is responsive, attentive, and aware of the human. This subtle yet powerful dynamic fosters trust, encourages adoption, and ultimately enhances both productivity and well-being in human-robot teams.
The Psychology of Safety
Psychological safety is usually discussed in the context of workplace culture — but it applies just as much to robotics. In human-robot systems, psychological safety means that workers:
Feel in control of the system,
Understand how it will behave,
Believe that it will not harm them,
Can speak up if something isn’t working.
Even physically safe systems may cause stress, hesitation, or outright rejection when these elements are missing. Robotics designers need to realize that psychological safety is not just a soft benefit — it is a hard requirement for adoption.
Consider:
A robot that moves suddenly without clear warning creates startling stress.
An exosuit that is hard to adjust may make workers feel frustrated and vulnerable.
A cobot that lacks clear signals may lead workers to overcompensate, slowing production or working around it.
Design choices are often the silent culprits behind these issues.
In How Design Makes Us Think, Adams points out that every shape, color, texture, and motion influences user perception. Robotics is no exception. From the curve of an exosuit’s back brace to the speed of a cobot’s approaching arm, users are constantly interpreting these cues — consciously or not.
If the robot’s design communicates control, reliability, and empathy, workers will sense it. If it communicates unpredictability or indifference, workers will back away.
Common Design Mistakes That Undermine Robot Adoption
Even with today’s advances, robotics developers often fall into familiar pitfalls. Here are the most common — and costly — mistakes:
1. Over-Engineering Without User Input
Too often, robots are built for pristine lab environments, not the unpredictable, cluttered realities of factories, warehouses, or fieldwork. A technically brilliant machine means little if it can’t function or adapt in real-world conditions. Early and ongoing worker involvement is essential.
2. Ignoring Discomfort
A robot that reduces strain in one area but creates pain elsewhere is a net loss. This is especially common in exoskeletons, where lower-back relief sometimes comes at the cost of new pressure points or restricted motion. Comfort is not optional — it’s make-or-break for adoption.
3. Overlooking Perception and Aesthetics
Design is communication. A robot that looks intimidating will be treated as such, regardless of how safe it is. Workers respond viscerally to appearance, motion patterns, and behavioral cues. Friendly, non-threatening design fosters trust and acceptance.
4. Forgetting Modularity and Adjustability
Workforces vary widely — in body size, work styles, and tasks. Fixed, one-size-fits-all designs rarely fit anyone well. Modularity and adjustability aren’t luxuries; they’re prerequisites for effective deployment across diverse teams.
5. Poor Onboarding and Training
A well-designed system can still fail if users aren’t trained effectively. Human-centered design extends beyond the hardware to the onboarding process. Workers need clear, practical training to build trust, skill, and confidence with the technology.
Design is the Real Differentiator
In the end, two companies could build robots or exoskeletons that are technically identical — meeting the same specs, passing the same safety tests, and offering similar performance on paper. Yet, only one may be fully trusted, adopted, and integrated into daily workflows. Why? Because of thoughtful, human-centered design.
Successful robotics isn't just about compliance or mechanical advantage. It’s about crafting systems that are comfortable, intuitive, and trustworthy — machines that not only work well but feel right to the people using them. As designer Sean Adams reminds us, "Design is not neutral; it always makes us feel something." In robotics, that feeling often determines whether a technology becomes a trusted partner or an expensive dust collector.
As robots continue to move beyond research labs into factories, warehouses, hospitals, and homes, this truth only grows more important: The best robot isn’t the strongest or smartest — it’s the one people actually want to work with.
Robot News Of The Week
Chef Robotics brings in $43M to deploy more food assembly robots
Chef Robotics raised $43.1 million in Series A funding to scale its AI-powered meal assembly robots, bringing its total funding to $65.6 million. The round includes $20.6M in equity and $22.5M in equipment financing.
Chef's robots have already produced over 44 million meals for major brands like Amy’s Kitchen and Sunbasket. Its AI-driven “data flywheel” helps improve robot performance as more meals are produced, accelerating customer adoption.
Founded in 2019, Chef focuses on food production, one of the most labor-constrained U.S. industries, with over 1 million unfilled jobs. Backed by Avataar Ventures and others, the company will use the funds to scale sales, marketing, and go-to-market efforts, while expanding into the U.K. by 2025.
Carbon Robotics adds autonomous tractor solution
Carbon Robotics has launched the Carbon AutoTractor, an autonomous system for existing tractors to help specialty crop growers address labor shortages and boost productivity. Powered by Carbon AI, it enables around-the-clock tasks like laser weeding, mowing, and ground prep. The system includes a bolt-on autonomy kit, remote control center, and advanced sensors, allowing operators to monitor and remotely assist when needed. Compatible with John Deere 6R and 8R tractors, it toggles between manual and autonomous modes. Growers can now run LaserWeeders 24/7, improving ROI and freeing workers to focus on higher-value tasks.
RIVR Robots To Begin Door-To-Door Deliveries In South Yorkshire
Barnsley residents will soon receive parcels from RIVR, a wheeled-legged robot. In partnership with Evri, the UK’s largest dedicated parcel delivery company, the robots will handle the "last-100-yard" segment of deliveries — the short, time-consuming trip from delivery vans to front doors.
This solution aims to boost efficiency, reduce driver workload, and address a major logistics bottleneck. Following the Barnsley launch, wider deployment is planned.
Founded in 2024 by ETH Zürich robotics experts and backed by investors like Jeff Bezos, RIVR is reshaping last-mile delivery with automation.
Robot Research In The News
A flexible robot can help emergency responders search through rubble
MIT Lincoln Laboratory and the University of Notre Dame have developed SPROUT (Soft Pathfinding Robotic Observation Unit), a vine-like robot designed to assist first responders in urban search-and-rescue operations. SPROUT can "grow" through tight spaces and debris, carrying cameras and sensors to map and explore collapsed structures without needing to cut new access points. Controlled remotely via joystick, the inflatable robot maneuvers around corners and obstacles, providing live video and mapping of hazardous environments.
Unlike traditional tools limited to straight paths or surface navigation, SPROUT offers a flexible, low-cost solution for navigating deep, unstable rubble. Tested with Massachusetts Task Force 1, the robot's design emphasizes ease of use, durability, and adaptability. The team is currently expanding its range from 10 to 25 feet and developing methods to map voids and assess hazards using data collected by SPROUT.
The project, led by Nathaniel Hanson and Professor Margaret Coad, aims to improve situational awareness for first responders while reducing risk. Beyond disaster response, the technology has potential military and infrastructure inspection applications. Ultimately, SPROUT could revolutionize how rescue teams understand and navigate dangerous environments before sending personnel inside.
These Electronics-free Robots Can Walk Right Off the 3D-Printer
Researchers at UC San Diego have developed a fully 3D-printed, electronics-free walking robot powered by compressed gas. Made from a single soft material and costing just $20, the six-legged robot walks, traverses sand, turf, and even underwater. Its motion is driven by a pneumatic circuit, similar to a steam engine, coordinating leg movements without electronics. Designed for environments where electronics fail, like radiation zones or disaster sites, the robot can operate non-stop for days when connected to a gas source. Future work includes integrating onboard gas storage, grippers, and using recyclable materials.
Robot Workforce Story Of The Week
How learning robotics opens the door for invention education
Robotics can seem intimidating, but parent Domi Flores-Wong says anyone can get started, even without prior experience. Speaking with News Hour Classroom, Flores-Wong shared how she and her husband began their journey when their son, Julien, joined a robotics team in first grade. “We knew nothing,” she said, “but there are so many online resources, especially for parents and educators starting teams.”
Julien, now part of the Cyber Tigers team from Kissimmee, Florida, recently competed at the VEX Robotics World Championship. He emphasized that robotics is all about learning through trial and error. “We started as a rookie team with a small robot and got pushed around,” he said. “But we learned from other teams, improved, and became a formidable opponent.”
Flores-Wong highlights that competitions like VEX aren’t just about winning but offer constant learning and inspiration. Aspiring students and parents can find plenty of free resources on the VEX Robotics website and by connecting with local schools or community programs.
“Perseverance and creativity are key,” says Julien. “You just have to start, learn, and keep building.”
Robot Video Of The Week
DHL Supply Chain and Robust.AI are shaping the future of human-robot collaboration — combining human strengths and robotic precision to unlock real business value and productivity.
Watch how they're redefining the power of working together.
Upcoming Robot Events
Apr. 23-26 RoboSoft (Lausanne, Switzerland)
Apr. 30-May 1 Robotics Summit (Boston, MA)
May 12-15 Automate (Detroit, MI)
May 17-23 ICRA 2025 (Atlanta, GA)
May 18-21 Intl. Electric Machines and Drives Conference (Houston, TX)
May 20-21 Robotics & Automation Conference (Tel Aviv)
May 29-30 Humanoid Summit - London
June 30-July 2 International Conference on Ubiquitous Robots (College Station, TX)
Aug. 18-22 Intl. Conference on Automation Science & Engineering (Anaheim, CA)
Oct. 6-10 Intl. Conference on Advanced Manufacturing (Las Vegas, NV)
Oct. 15-16 RoboBusiness (Santa Clara, CA)
Oct. 19-25 IEEE IROS (Hangzhou, China)
Nov. 3-5 Intl. Robot Safety Conference (Houston, TX)
Dec. 11-12 Humanoid Summit (Silicon Valley TBA)